Instructions on how to create physical, repeating textures you can FEEL and TOUCH on your 3D prints, using a new feature found in SOLIDWORKS 2019. (And this technique will work with ANY type of 3D printer, not just Stratasys!)
We've talked before about how to create similar displacement-mapped models for 3D printing in Rhino. I've even shown how we can create beautiful, full-colored and displacement-mapped prints using Photoshop, which is a little easier.
Now we're going to look at a new tool in SOLIDWORKS 2019, called '3D Textures,' which makes things even EASIER:
Recipe costing software for mac. Recipe Costing Software is the only off the shelf back office suite with it’s own restaurant point of sale. Start with food costing, build recipes, sub recipes, and do a.
Let's get started.
simulating leather textures on cosmetic automotive parts:In the real world, these automotive parts are mass-produced by injection molding, and the leather texture added by acid etching the INSIDE of the injection mold, which adds more expense to an already expensive mold-making process.
But what if an automotive engineer wants to see an early mock-up of what their part MIGHT look like, WITHOUT paying for an entire mold to be cut out of aluminum first?
Tamil christian songs download free. That's where 3D printing comes in. And the first thing we're going to do is define the area we want the 2D texture applied to.
Now I'm specifically going to make this harder than it needs to be, by using the Split Line command in SOLIDWORKS, to carve out certain areas I do and don't want textures on.
(I could skip it for my sample part, but if I teach you this step now, you'll be ready for anything in the future.)
So let's say we wanted a 'safe' circle around the hole at the top of my part, an area that won't get textured. We'd sketch a circle around that hole and use the Split Line command to make it two separate faces:
This can be done with any type of shape you can sketch, not just a circle.
I went ahead and did this two more times on my part to create 3 total safe zones:
If you need more info about the SOLIDWORKS Split Line command, click here.
Now let's apply a 2D texture. There are about 15 ways in SOLIDWORKS to apply an appearance to a face, but I'm going to use the 'Edit Appearance' icon right in the middle of the screen:
Choose your desired faces as targets on the left, and it works better if you choose one of the black and white '3D Textures' as your source on the right:
(Why black and white? Remember, as we discussed in my other displacement mapping tutorials, white areas will be extruded UP away from the surface, and the black areas usually DOWN into the surface, or kept flat. So you want good, sharp, contrast between black and white.)
There wasn't a pre-existing leather texture in the SOLIDWORKS library so I just used 'Bubble'. (And notice how our safe areas remain untouched by the texture.)
Now we're going to use a new feature in SOLIDWORKS 2019 to displace this texture into actual 3D information we can feel.
'3D Textures,' found under 'Insert.. Features..':You choose the body you want to change (the only body we have, in our case), and now you've got a lot of settings for how far the texture will displace from the surface, how much to refine the underlying mesh, etc.:
(And I don't know why the name 'bubble' is misspelled when using the library's own texture.)
You have to click on the checkbox next to each face to make that face's texture displace, and the 'Refinement' level seems to affect how fine a mesh is made under each shape from the original texture:
Notice that our safe faces aren't bumped, and that even the 0% refinement face has some waviness to it, which is not what I expected.
After hitting the green check mark, your textures are visually shown on your SOLIDWORKS part and in the feature tree, but you need to do one more step before they are real enough for 3D printing:
(For more information about SOLIDWORKS' new '3D Texture' command, click here.)
Finally, to make these visual textures into something 3D printers can read, we have to 'Convert them into a Mesh Body.' Right click on a solid body in the feature tree to see the command:
There seem to be choices on how fine the conversion is, and just like any STL export, the finer you set the sliders, the larger the file. (We'll take a look at what the 'right' settings are later.)
Hit the green check, and if you save that resulting body out as an STL (for printing), you'll notice the file size might be pretty large:
That's because the hundreds of thousands of little triangles needed to describe all the bumps and waves we just put into the body require data in the STL, making it huge.
Normally I'd go back and change some of those sliders because a part this small shouldn't need a file size that large, but I wanted to see what happens.
So I printed it.
But now the other side of the coin.
THE BAD:
It definitely matters what orientation you print the bumps in, and it seems a vertical face definitely works much better than a horizontal one:
To put it another way, due to how current FDM technology puts layers down (one at a time, vertically in the Z), one orientation will work much better than the others for your 3D textures.
I made up another simple 24 (!) MB part, textured with fancy bowties to illustrate the concept:
So theoretically, the bowties should be fine on vertical faces, but print very poorly lying flat.
Of course, we don't do anything just theoretically here in these tutorials, so I printed these too.
And can we talk about how much cooler FDM prints look with a simple texture on them? If those blocks had been normal flat rectangles, I wouldn't have cared to obsessively watch the printer. But with textures applied:
Even a simple texture seems to give an FDM print much more depth, more complexity and more psuedo-realism than before. I might do all my FDM printing with textures from here on out if possible!
So how did the printing angle affect our bow ties? Let's see if you can tell which was which:
Obviously something is going on with print C, and to a lesser extent, print B.
But to figure out WHY, we have to talk about how FDM beads are laid down:
That's an oversimplification, the rastering process is much more complex than just switching directions every layer, but it's good enough for our example.
The main point is, your layer height is fixed (I was using 0.010', or 0.254 mm, for my quick prints). But a moving print head can make much smaller changes in X or Y:
(On the printer I was using, those green subtle head adjustments can often be 10x finer than the layer height. So we're starting to see the issue.)
Secondly, when printed flat to the tray, my bow tie textures were 0.200' wide but only 0.020' tall:
So at my 0.010' layer height, my printer would only have 0.020'/0.010' = 2 data points (layers) to approximate the complex profile of a bow tie. Have you ever tried to approximate a complex shape with only 2 data points?
It works out pretty much like this:
And that's exactly what we see in the final print:
But if we print those same textures on a VERTICAL face, that means we have 0.200' / 0.010' = 10 layers to capture the shape instead of 2, and each vertical layer can just make subtle head changes to shape the texture out from my wall:
And if you look at the actual prints side by side, that's exactly what we see happening:
You could have seen this in GrabCAD Print's slice preview as well:
There are other trigonometric reasons the resolution gets worse, the closer a texture gets to horizontal, but that's good enough for now. (And if you really want the deeper explanation, email me at shuvom@grabcad.com with an example in mind!)
But we've learned our lesson: keep those textures vertical for best results!
So let's put that to use in one last print.
So how did it turn out?
Awesome.
This was a hex pattern like a golf ball might have, and with barely any extra work, I had my 3D printed part looking amazing detailed! It totally changes the aesthetic.
Look how that texture wraps around that fillet. And our safe zones around the hole and edge are still respected.
Touching this part is now a feast for the fingers!
Here's what I love about this process:
1. It's super easy. The changes in SOLIDWORKS to put on this hex pattern were 4 features which took less than 2 minutes. Remember your '3D Textures' and 'Convert to Mesh Body' commands, and you'll be fine.
2. It's super controllable. With the 'Split Line' command we covered earlier, it's possible to put these textures in exactly the areas you want them, and protect the areas you don't. And with growing skill at texture mapping in SOLIDWORKS, you can even start to go around corners, like our fillet above.
3.It prints well if you use the right settings. As long as we don't try to print a texture on a flat horizontal face (or something with a lot of overhang, leading to a lot of support removal) we should get good enough resolution to get the affect we want. Other co-workers have tried printing at angles as low as 5 or 10 degrees, but I'll probably stay above 45 if I can help it, with 90 degrees from horizontal being the best.
(Also, a depth of 0.020' on the texture works fine at 0.010' layer heights. I'm going to stay at 89%+ refinement for now, and I'll play with the STL export settings to see if I can reduce STL size while not affecting outcome. But for now, prepare for 20-100 MB files for textured parts that fit in your hand.
Co-workers have told me that, for printing entire textured car dashboards or aerospace cabin interior parts, their STLs sometimes get up to 2GB (!!!) in size, so if you're in that range and the part is taking FOREVER to slice, maybe reduce the refinement and STL export settings, or split the part into multiple prints. But that's the subject for a future tutorial, if people want.)
4. And best of all, since we're just exporting STLs from SOLIDWORKS, it will work with any type of 3D printer!
I used a Stratasys F370 to make the prints shown above, but could have used our old uPrint, Dimensions, or even our full-color J750 to get some really cool results. (Or even our competitors' machines- shhh!)
So I've think I've found an easy way to add a lot more realism to my FDM prints!
If you want more info on the Stratasys printers used for these parts, click here, and if you have any questions about the texturing process, let me know in the comments or at shuvom@grabcad.com.
Hope this helps make your prints more useful!
With the recently released SolidWorks 2019, we can now add 3D Textures to parts and even 3D print them. Highlight the face (s) that you want to add the texture to and then go to edit appearance. On the Right side of the screen, open the “Miscellaneous” folder and select “3D Textures” 4.
For the longest time, it felt like the terms “SOLIDWORKS” and “3D printing” were rarely discussed in any particularly paired light. Sure, we conceptually understood that SOLIDWORKS was a mechanical design tool used to make 3D designs. We conceptually understood that a 3D model was needed to 3D print a design.
It just felt like there should be more integration (and more awareness of pre-existing integration) between one of the most important 3D CAD tools on the market and emerging manufacturing techniques.
A couple of years ago, I aimed to educate SOLIDWORKS customers and prospects on pre-existing integration with 3D printing technology by creating a custom infographic. This infographic laid out, in chronological fashion, all enhancements witnessed in each SOLIDWORKS release in regard to 3D printing.
This infographic, created during the SOLIDWORKS 2017 release cycle, can be found here. But as 3D printing passes through its own adoption curve in production settings, I recall feeling there could be so much more integration of 3D printing in SOLIDWORKS. I felt this even as I was making an infographic cataloging a fair amount of integration over the years.
A screenshot from my video below, in which I discuss how to add 3D texture to an object in SOLIDWORKS.

In SOLIDWORKS 2019, one of my favorite design enhancements is actually one that befits 3D printing applications more than any other. The “2019 What’s New” documentation labels this enhancement: Transforming Textural Appearances with the 3D Texture Tool.
Try saying that 10 times fast.
So, what does this mean, exactly? It means, in short, that designers of any skill level can now easily apply patterned physical textures that used to be difficult to create, both for SOLIDWORKS and the person using it.
Take the knurl, for instance. At my first engineering job out of college, I remember an email chain going around prompting members of our CAD design team to create a knurled pattern in SOLIDWORKS in the fewest possible steps.
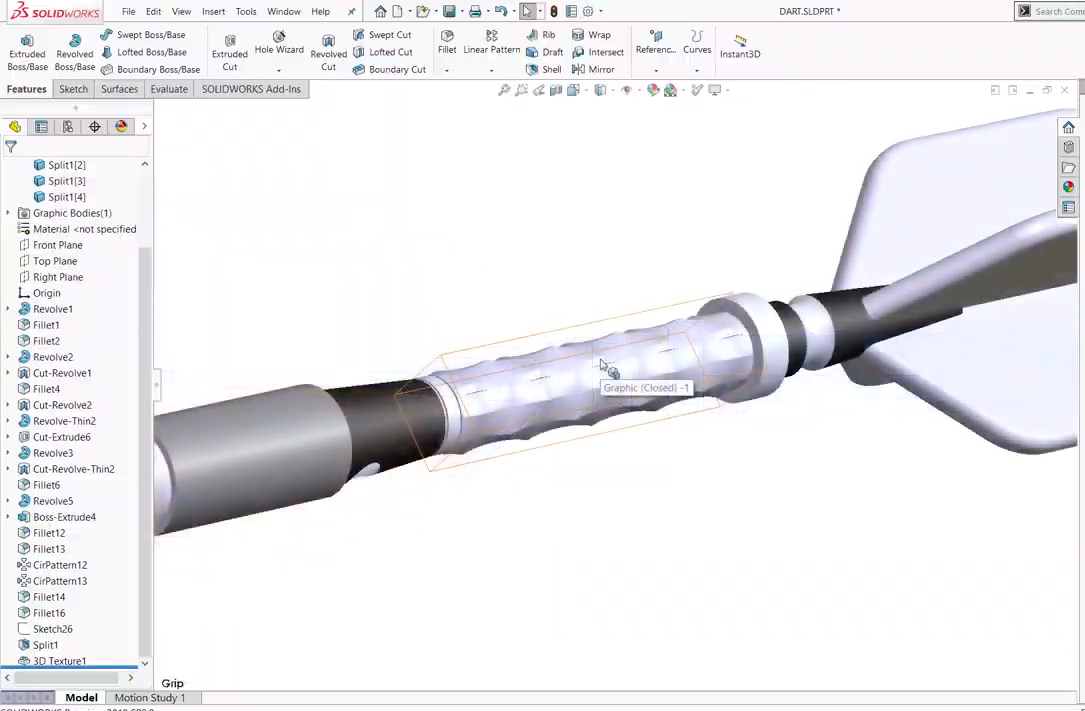
There were two inherent challenges. 1) Knurls are fairly complex to model — especially if your aim is to model them accurately across curved surfaces, and 2) Because of their faceted nature, a patterned knurl feature across a curved surface would typically take SOLIDWORKS a longer-than-usual time to present the geometry during feature rebuilds.
How To Add Texture Solidworks
Many of us took our best shots at the task. People like myself, Toby Schnaars (Model Mania champion), Neil Sardinas (20+ years of SOLIDWORKS experience), and Brad Snow (CAD/FEA expert, former Analysis Services Manager at our company) deeply contemplated the modeling challenge and gave our best takes on a solution.
Add Texture To Solidworks Part

How To Add Texture Solidworks
Sure, it was fun to pick each other’s brains. A great learning experience for me, no doubt. But, ideally, do you think creating such a pattern should require multiple tries from various CAD design experts? Maybe not.
In the video below, I’ll show how you can take grayscale heightmap images (don’t worry – I’ll explain what these are!) and use them to create a 3D texture in SOLIDWORKS 2019. This makes the situation I just described a whole lot easier!
If you have any questions on the functionality after watching this video, please give me a shout on Twitter (@ServicePackSean)! I’d be glad to discuss.